In the world of construction and design, the use of curved shapes adds a unique aesthetic and functional appeal to any project. One of the best ways to achieve such curves is through the use of plywood curved concrete forms. These forms allow for precision in casting concrete into beautiful, flowing shapes. In this article, we’ll explore how to create smooth curves using plywood forms, from understanding the basics to troubleshooting common issues.
Understanding the Basics of Plywood Curved Concrete Forms
Before diving into the practical aspects of building plywood curved concrete forms, it’s important to grasp the fundamental concepts behind them. Curved concrete forms can be used for a variety of applications, including sidewalks, sculptures, and even structural components.
The science behind these forms lies in their ability to withstand the pressure of setting concrete while maintaining their shape. Understanding the mechanics of how the materials interact is crucial for ensuring the durability and smoothness of the final product.
The Science Behind Curved Concrete Forms
Curved forms distribute the weight of wet concrete evenly, preventing any stress points that might cause cracking or distortion. The key is to ensure that the curves are formed gradually rather than abruptly. This minimises the risk of structural weaknesses and improves the aesthetics of the finished form.
The material choice plays a significant role in how well the form performs. Plywood, for instance, is flexible enough to be bent into curves, yet sturdy enough to provide support. The combination of these properties makes plywood an ideal choice for crafting concrete forms.
Choosing the Right Plywood for Your Project
When selecting plywood, it’s essential to consider the thickness and the type of plywood best suited for your project. Typically, a thickness of 3/8 to 1/2 inch is adequate for most applications, providing the necessary strength without being too difficult to bend.
Moreover, opting for exterior-grade plywood is advisable as it can withstand moisture better than standard plywood. This is particularly important if your concrete pouring activity involves wet conditions, which is often the case in outdoor settings.
Preparing Your Workspace for Plywood Curved Concrete Forms
A well-prepared workspace is crucial to the successful creation of curved concrete forms. Not only does it ensure that you have all the necessary tools and materials at hand, but it also creates a safer environment for working.
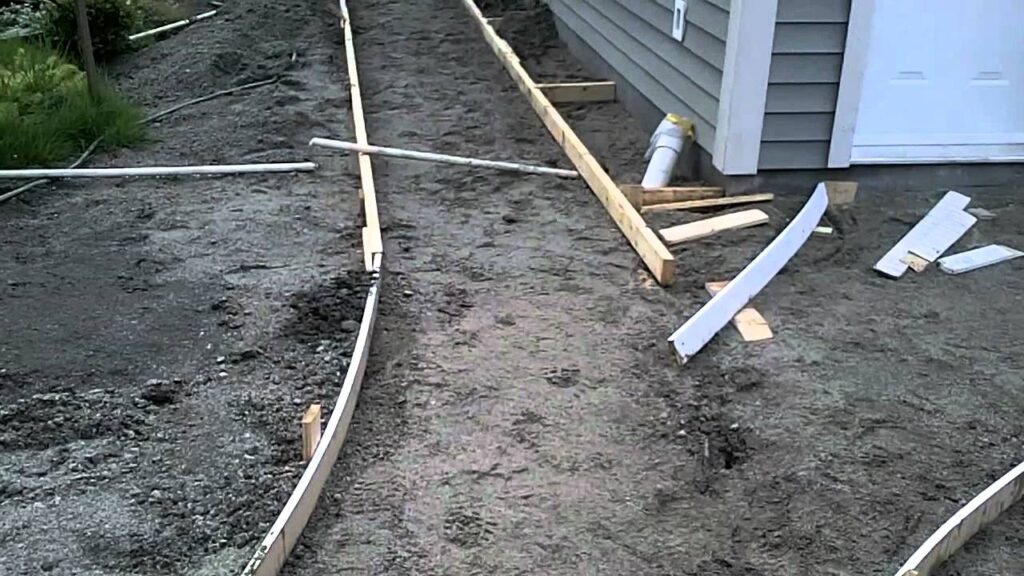
Necessary Tools and Materials
To start, you’ll need the following tools:
- Jigsaw or circular saw
- Measuring tape
- Wood clamps
- Sandpaper or a sander
- Protective gear (gloves, goggles)
In addition to these tools, gather all the materials needed for your form, which include plywood sheets, screws, and wood glue. Ensuring everything is within reach will let you work more efficiently.
Safety Precautions to Consider
Safety should always be a priority when working with power tools and heavy materials. Make sure to wear protective goggles and gloves to prevent any injuries. Additionally, check that your workspace is free from hazards that could lead to accidents.
It’s wise to have a first-aid kit readily available, just in case. Simple steps like ensuring your tools are in good working condition can go a long way in keeping you safe during the project. Click here to find more about first-aid kit.
Step-by-Step Guide to Creating Plywood Curved Concrete Forms
Now that you’re prepared, let’s walk through the step-by-step process of creating your plywood curved concrete forms.
Cutting the Plywood to Size
Begin by measuring the dimensions of the curve you wish to achieve. Use a measuring tape to outline the desired shape on the plywood. A consistent method is to create a template using cardboard first, which can help in visualising the final outcome before committing to the plywood.
Once you’ve marked your design, use a jigsaw to carefully cut along the lines. Ensure that you follow the curves smoothly to maintain the integrity of the form. Remember, sharp blades cut cleaner and reduce splintering.
Shaping the Plywood into Curves
Bending the plywood into curves can be done using steam or soaking methods to make it more pliable. This is the key to achieving a smooth, flowing curve without breaking the plywood. Once it’s flexible, clamp it into the desired shape and allow it to dry while secured, ensuring that it retains that shape permanently.
For different radii, consider using thinner strips of plywood, which are much easier to bend and can be laminated together for additional strength.
Assembling the Concrete Form
Once shaped, it’s time to assemble your form. Connect the pieces using screws and wood glue, ensuring that everything fits snugly. This helps prevent any leaks when pouring concrete. You may choose to line the interior of the form with plastic sheeting to aid in the removal of the form post-curing. Read more about plastic at https://www.canr.msu.edu/news/what-is-plastic
Before pouring concrete, it’s wise to double-check the alignment of the form and ensure it’s secured to the ground. This prevents shifting during the curing process, which could compromise the final shape.
Tips for Achieving Smooth Curves with Plywood Concrete Forms
Now that you’ve created your forms, consider these tips for ensuring your curves remain smooth and visually appealing.
Techniques for Bending Plywood Without Breaking
To successfully bend plywood without breaking, employ the use of jigs, which can assist in holding the wood in place as you apply heat or moisture. This technique not only helps in achieving the desired shape but also prevents any damage to the material.
Be patient throughout this process, as rushing can lead to mistakes. Take your time when applying pressure and allow the plywood to acclimatise to its new form.
Ensuring a Smooth Finish on Your Concrete Form
Achieving a smooth finish on the concrete itself relies heavily on the form. Sand the plywood until it’s smooth, which in turn will help you achieve a flawless surface on the cured concrete. Additionally, consider using a concrete release agent on the form to facilitate easy removal and minimise surface imperfections.
After pouring concrete, tap the form gently to release any air bubbles, ensuring a solid and smooth surface once cured.
Troubleshooting Common Issues with Plywood Curved Concrete Forms
Even with careful planning, challenges can arise. Here are some common issues and how to effectively deal with them.
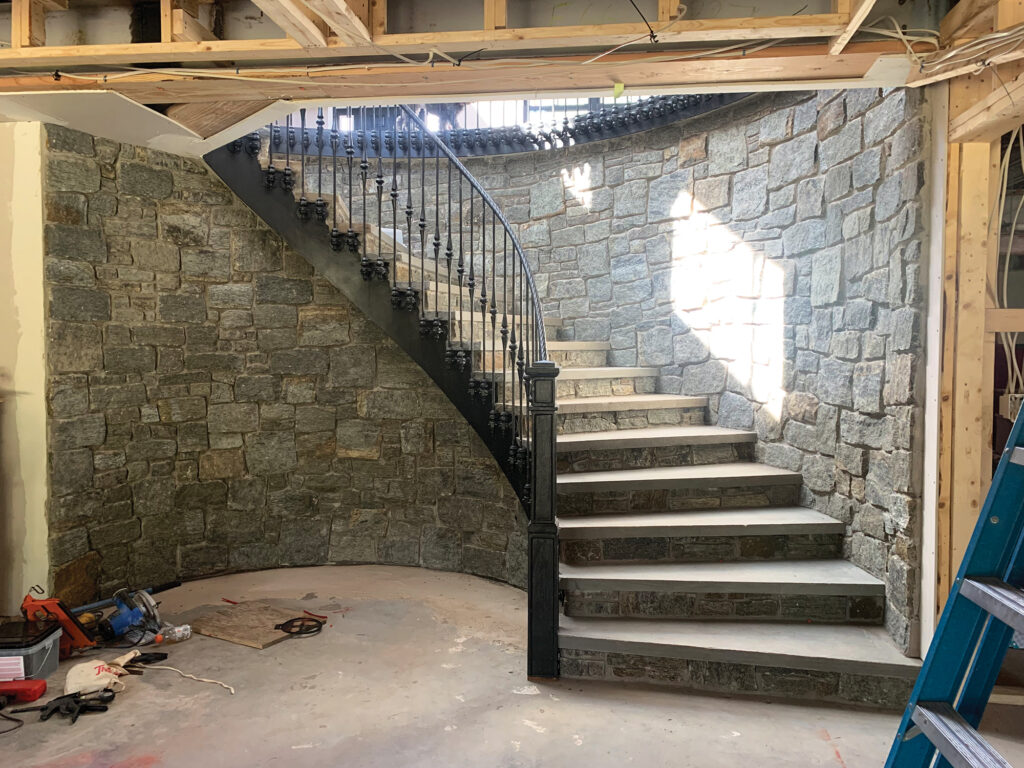
Dealing with Plywood That Won’t Bend
If you find that your plywood isn’t bending as expected, it may be too thick for the desired curve. In this case, consider either reducing the thickness or applying additional moisture to facilitate bending. Additionally, if the wood feels too stiff, allowing it to sit in warm water for a short period can help.
Fixing Uneven Curves in Your Concrete Form
If you discover that there are uneven curves in your finished form, it’s not the end of the world. You can use a planer or sanding block to smooth out the uneven areas before pouring the concrete. Alternatively, if the concrete has already been poured, consider using a concrete grinder once cured to even out the surface.
In conclusion, creating smooth curves with plywood curved concrete forms is an accessible and rewarding process. With the right tools, materials, and techniques, you can achieve beautiful, functional results that enhance any design project.
Other resources: Choosing the Right Concrete Form Plywood for Your Project